From the Rod to the Mouth - How DESS® abutments are made
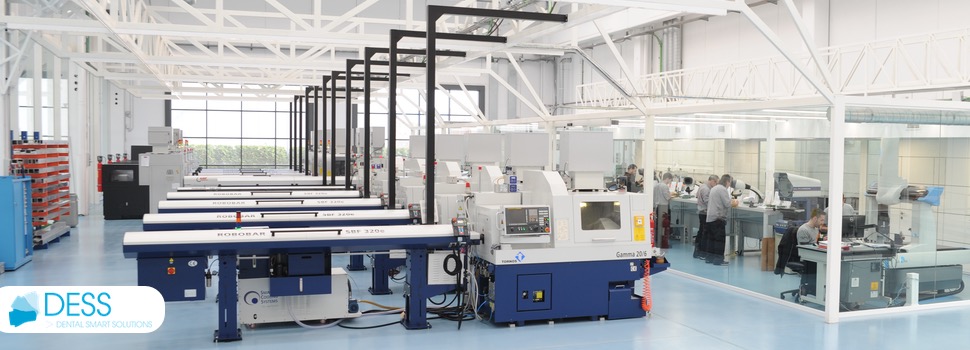
Our history begins many years ago, when we started producing small precision metal parts in the 50's in a small workshop in the center of Barcelona. Over the years, the company adapted to the times and in 2007 the first outsourced production in the dental sector took place.
Then, in 2009, we registered the trademark "DESS® Dental Smart Solutions" and the rest, well, is history.
Let's take a look at the machines that manufacture our compatible abutments and even dental implants. I think it is worth explaining the core of the process that takes place with turning machines, or lathes. Of course, this applies to any other manufacturer of dental implants and prosthetic abutments.
So, what is a turning machine? Well, the principle is very basic. A lathe is a turning support (spindle) that spins whatever material (clay, metal, wood) and in turn holds a tool, or even human fingers if using clay, removing material until the final shape of the part is achieved.
Source: Pinterest
Perhaps the very first lathes were used to shape clay into pots. Later, someone probably attached to the spinning table something stronger than a human foot and leg. After that, the first wooden parts, for example, could be made.
Let's now jump back in time to when the lathes used for metalworking were powered by steam and belts, as shown in the picture:
Source: Pinterest
As soon as electricity arrived, lathes adopted this power source and the parts could be moved by electric motors while the operator, with the help of wheels, pinched the rotating part with the tool. In this way, parts could be produced much more quickly.
Manual turning machine from DESS® headquarters 2022
Next, I hasten to talk about the ones I want: the "Swiss" lathes, named after their country of origin. These have a special feature: the spindle that grips the rod through it can move back and forth and not just rotate. That allows you to shape long, narrow parts without losing precision. These machines are perfect for manufacturing dental implants or any long abutment, such as an analog.
However, the first machines appeared long before computers. They were automated by a spindle and cams that pushed the tools like cams push the valves of a car engine.
If you want to see how these "old legends" move, you can find many videos on YouTube. I've copied some links here, but don't panic, ours are newer than those and the factory look is also quite different.
Once CNC (Computer Numerical Control) came on the scene, the cams were replaced by actuators or electric motors, making switching between programs child's play compared to the past, where each cam had to be profiled to get the movement of each tool at the right time. This was an art learned and applied by my grandfather, my father and even my brothers.
Early CNC machines in the 1970s had to be programmed with punch cards. In the 1980s that was replaced by more capable computers that could be programmed on-site, in front of the machine screen, or via RS232 serial connections from any computer.
We bought the first one around 1990 or so and it was a turning point, never better said, for the fate of the company as within 10 years all our machines were CNC and we got rid of the old ones.
The first one we bought was a top-of-the-line Japanese Okuma LB15 that even had a color screen. What more could we ask for? That machine was solid and reliable like no other. It confirmed one of our long-held beliefs: never cut corners on production equipment. Since then, we have always purchased the best to produce everything we do.
The time has come to talk about the companies that dominate the world of machines that produce dental implants and their abutments. Everyone knows the major implant brands: Nobel Biocare®, Straumann®, Zimmer®, Astra Tech®, etc. Just as everyone who produces knows that there are only a handful of machine brands to use, let's get to know them a little.
- TORNOS
This Swiss company is probably the father of all machine and tool manufacturers. It's not the biggest, but it has maintained its solid reputation over the years. Tornos was founded in 1914 and is now probably the smallest of the "big four". It has more than 700 employees and a clear global presence. Tornos is a company that, thanks to its tradition combined with innovation, deserves its prestige.
It is one of the few remaining producers of multi-spindle lathes that can handle up to 5 bars at a time. These machines are not so suitable for dental work, but they are ideal for large batches destined for the automotive or electronics industry.
- TSUGAMI
Tsugami is a company that started in 1923 near Tokyo. It currently employs more than 2,800 people and has factories in Japan and China. Its machines are especially known for their extreme reliability. They are bulletproof and as robust as tanks.
My opinion is that they may not be as innovative or productive as Tornos or Citizen, but their machines are stable and require almost no maintenance. This is paramount and gives the greatest peace of mind to the producer. And that is gold.
- STAR MICRONICS
This is the second of the three Japanese manufacturers. They started, by happy coincidence, the same year our grandfather created his company. However, Star has gotten a little... bigger, as they now have over 1,500 employees worldwide! For more information visit their website.
The funny thing about them is that they are still producing printers which was probably a big business years ago, and now it is a niche business, but still interesting for them. They make small specialized printers for retail businesses.
- CITIZEN
Last, but with over 2,000 employees in total, certainly not the smallest! They were founded in 1930 to manufacture watches and started making their own tooling in 1936 and CNC machines in the 1970s. Once they acquired another highly reputable company, Miyano, in 2010, Citizen Miyano became what it is today.
To me, their leadership in bushings technology for tool movement is remarkable. They use linear magnetic motors that achieve incredible speeds and position feedback. They are probably now, along with Tornos, the two reference brands for watchmaking.
Now you know what a lathe is, the machine behind every dental implant and abutments. Now you also know who is part of this industry. In the next post, I will tell you what machines we have.
I have not created this post to be a technical article, just to share a bit of my experiences in this industry as I have played among these machines since I was 10 years old. I hope you liked it and learned a little with this short read.